Sort + Filter
Anti-Friction Coatings and Solvents
Anti-friction coatings are an innovative and easy-to-use solution for long-term dry film lubrication and surface protection.
Anyone who repairs industrial equipment knows that lubrication is essential for proper operation. When wet lubricants fail, it's time to evaluate anti-friction coatings. This dry lubricant simplifies maintenance and extends the life of a wide range of equipment and surfaces.
What are sliding coatings?
The range of anti-friction coatings is a high performance, all-in-one solution for long-term lubrication. These solvent and water based products contain a range of solid lubricants and additives to reduce friction and protect metal, plastic and elastomeric surfaces.
The products are evenly applied to the surface and cured to a dry, paint-like coating. This low-friction coating has many advantages, but may not be the right choice depending on application requirements.
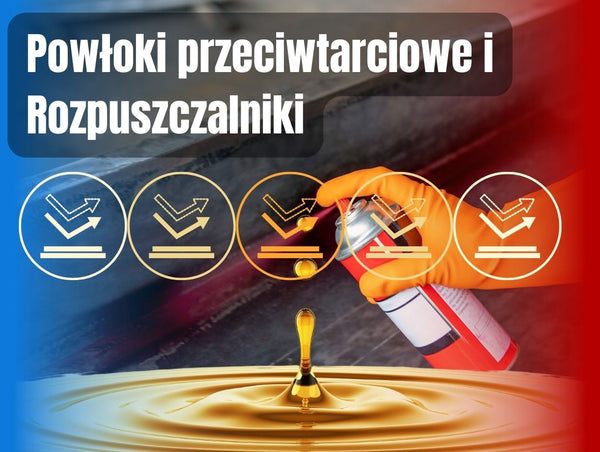
Where and why to use anti-friction coatings?
Dry films provide a shield against contamination from dust and dirt while providing solid protection against wear and corrosion.
- Easy to use
- Durable dry coating
- Protects against dust and dirt
- Reduces noise, vibration and harshness (NVH)
- Helps prevent corrosion and rust
- Protects metal surfaces against wear, damage and pitting
- Reduces friction
- Prevents stick-slip
- Low noise, vibration and harshness
- Durable wear protection
Applications
- General Industry
- Production equipment
- Aviation and spaceflight
- Oil and gas refinery
- Food and beverage production
- Agriculture and construction
- Exercise equipment
- Household and commercial appliances
The table below helps illustrate the benefits and limitations of the AFC products we offer.
Benefits |
Limitations |
|
|
Coating application method
The solvent-based coating is designed for maximum flexibility and is easy to apply using a variety of methods and can be applied by a variety of processes including spraying, brushing, dipping, spinning, screen printing and roller coating.
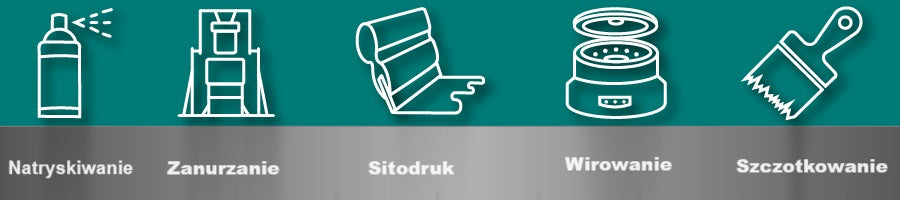
How is a slip coating applied?
To ensure a uniform and durable coating application, it is recommended to thoroughly clean the surface by degreasing, sandblasting, phosphating, anodizing, acid cleaning and alkaline detergent cleaning. Each of these methods is recommended to effectively prepare the surface for coating application.